WHAT IS ROTARY BROACHING?
Signature Series Rotary Broach Holders & Tools
Rotary broaching, also known as wobble broaching, is a machining process that puts non-round holes into parts using cutting tools with shapes that mirror the desired hole geometry. The tool's longitudinal axis is offset from the workpiece's axis by 1 degree, which creates the "wobble" as it spins. The wobble causes the broach to cut into the sides of a pilot hole as it is driven into the workpiece, creating the desired non-round holes on either the inside or outside of a part.
On a machining center, the broach holder revolves in the spindle while the tool and part are stationary. This is the opposite of how one is positioned on a lathe where the part rotates synchronously with the tool while the holder is held in an end working position. The operation takes only seconds and can eliminate a secondary operation, as a result the part may be produced completely in one setup.
The broaching holder serves two functions: It holds the broach tool in a free spinning bearing and places it at a 1-degree angle relative to the centerline of the workpiece. The face of the broach tool is the apex of the 1 degree and is located on the same centerline as the workpiece. A 1½ -degree clearance angle is built into the tool and while the tool advances forward in a wobbling motion, each tooth cuts the same groove with a scalloping effect as it rotates in and out of the leading point position. This is similar to a wobbling coin, only one point is touching at any given time, greatly reducing the amount of force needed to form the shape.
Broaching tools are used as tools - broaching mandrels. The shape, construction and material of the broaching tools guarantee high precision and quality of machining of parts by the technology of metal chip processing.
Broach tools also improve productivity by removing work from a machining center, allowing a machinist to complete the broaching operation while another part is in the machine. In other cases, special rotary broach tools can be used inside a machining center or lathe. These tools allow the creation of internal polygonal shapes like those on socket head screws or Torx screws while the machine operates.
GenSwiss offers hex broaches, square broaches and hexalobe broaches, as well as custom sizes and forms. Broaching tools can be designed to cut internal or external surfaces.
Please do not hesitate to call 413-562-4800 or email [email protected] with rotary broaching application questions or if you need help deciding which tools are right for your job.
ADVANTAGES OF ROTARY BROACHING
-
- Faster cycle time and accuracy
- No secondary operations required
- Adjustment free for minimal setup time
- Reduced stress increases tool life
- Lower machine mainenance cost
- Broad range of materials
- Ability to produce difficult-to-machine features
- Holders can be used on a variety of machines and feature precision centering adjustment
- Broaches cut equally as well in right-hand or left-hand operations
- Economical when achieving quality of finish and close tolerances
VIDEOS
WHAT ARE THE BEST CASE USES OF ROTARY BROACHING
Broach holders and tools are engineered and manufactured for applications that require high tolerance and precision surface finish particularly important to the automotive, aerospace, and medical industries, all of which require a high degree of accuracy. The compact design combined with a medium-duty bearing provides a more rigid setup to withstand the increased pressure generated when broaching titanium and other high-strength alloys.
Broaching is Intended for use in Swiss Type Lathes and Gang Style Lathes that are accurate to the work centerline within a few tenths of a thousandth. Capable of creating hex broach forms anywhere from .040" - .375" these broach holders can handle nearly any size required by the Swiss Machinist.
Fast-setup rotary broach tool holders greatly reduce setup time and enable less experienced operators to utilize rotary broaching in their setups. Conventional rotary broach holders featuring directional centering and heavy-duty bearings are also available for larger machines such as turning centers and vertical machining centers.
Broach Tool Grades HiCo8 - 2110 & 2122 Series Tools: Ideal for Medical materials; IE Titanium & Stainless - Imported from Switzerland Commercial Grade HSS - 2000 Series; SAE and Metric Standard sized hex broaches for free machining materials such as 12L14, Aluminum and Brass.
Broaching is a fundamental machining operation for machine shops of all sizes. It is still a critical process for high-volume automotive manufacturers and makers of complex turbine components. It likewise will remain a common operation at maintenance shops when internal keyways or polygonal shapes are needed for repairs.
ROTARY BROACHING GLOSSARY TERMS
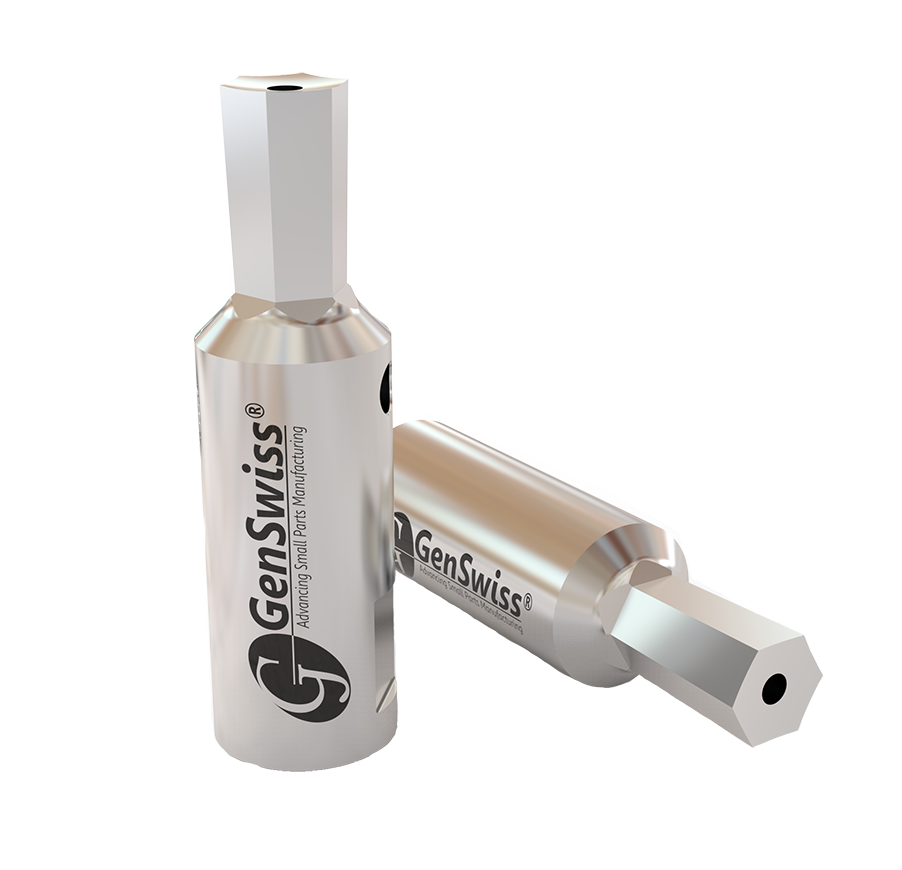
Broach: tool used to produce inner and outer profiles, whereby a multi-toothed tool removes Material from the workpiece. The benefit of this process includes a high Cutting capacity, excellent surface quality and dimensional accuracy. The tool performs linear or rotary cutting movements.
Broaching: machining process in which a broach is pulled or pushed through a workpiece or along the surface of a workpiece to generate a final shape. Inner and outer profiles Broaching is used extensively in machining gears, holes, splines and keyways.
Broaching Operations: classified as internal broaching and external broaching (also known as surface broaching) based on the machining surface of the workpiece.
Cutting Fluids: used to cool the workpiece and broach, to lubricate cutting surfaces, and to flush the chips from the teeth. (see more on Swiss Silver Cutting Oil)
Die Broaching: uses a broach to cut externally on the component for high volume production.
External Broaching: used to create profiles (Gear segments). This operation is ideal for parts that are identical for the entire circumference of the part. Ideal parts for this application would be for example, faucet handles, automotive wiper blade axles, splines, hand grips on the OD of the part, and wrench flats. Typically, tolerances can be held to within a .003-.005.
Hexagonal Broach: features a dished cutting face and vent holes for relieving hydraulic pressure. Two overall lengths are available to the market, 28 and 32 mm, with hexagonal cutting features ranging from 1.5 to 10 mm in diameter.
Internal Broaching: used in cases where the inner and outer contours of a workpiece cannot be created by means of Milling or Turning. The most common application is the broaching of inner profiles using an internal broach to produce keyways, multi-edged opening, internal gears.
Internal Broaching: used for machining interior surfaces such as round holes, splined holes, and irregular shaped holes.
Punch Broaching: uses a broach to cut internally in the components. Punch broaching is used for high volume production.
Rotary Broaching: the broach and the workpiece rotate together. The broach moves into the workpiece making successive cuts. Rotary Broaching or Wobble Broaching is economical for smaller production runs.
Shaping: sometimes called slotting - is a machining process where the workpiece is secured on the machine table and advanced into the path of a reciprocating ram, upon which is mounted a single-point cutting tool. Shapers are typically used to cut internal shapes and forms, such as keyways, slots, squares, hexagons and straight-sided splines.
Special Broaching Operations: such as punch broaching, die broaching, single point broaching are used when the broach shape cannot pass all the way through the workpiece.
Square Rotary Broaching: creates, in one pass, a square hole in a previously cast or drilled round hole commonly found in custom sockets, shaft extensions, and hardware components.
Surface Broaching: used for Machining Exterior Surfaces such as flat, concave, convex, serrated, or cam-shaped profiles.
ROTARY BROACH HOLDERS
Rotary broach holders are intended for machines that are more accurately centered, such as Swiss-type screw machines and gang lathes. These holders are on-center and take less than 3 minutes to set up. The broach head places a qualified tool on center with the part, taking no more time to set up than a standard ID tool. The design allows tighter tolerances to be held, while simplifying set up.
Ideal for CNC Swiss Machines such as Citizen, Star, Tsugami, Tornos and other models.
2160 Series Rotary Broach Holder
The 2160 series Swiss-type rotary broach holder is the premier choice for performing broaching applications in your Swiss-type CNC machine or gang-style lathe. Able to fit into nearly any tight tooling configuration this broach holder solves tooling problems and increases productivity by eliminating secondary broach operations. Field proven and used for years by the Medical Implant as well as Aerospace manufacturing industries, this broach holder has a maximum diameter slightly larger than an inch and a head length of slightly smaller than 2½ inches to the tip of the broach. The recommended profile size range for this holder is .050” to .375”.
It easily fits into machines with the tightest tooling layouts and comes with an extended tool shank allowing it to be cut shorter for machines with limited space. The proprietary bearing is able to withstand more than 2,000 pounds of thrust. This is an ideal condition for tough materials such as titanium jobs. You can use it for subspindle work, or use it in any ID turret station and not worry about being off center.
KEY FEATURES
-
- No center indicating required
- Ideal for medical & aerospace fastener applications
- Low profile; fits machines with minimal interference
- Shank length is customizable, no need for bushings
- Short head length is ideal for sub-spindle applications
- Longer OAL broach tools can be used by adjusting X-axis
2160 Series Flange Mount for STAR Machines
6180 / 6181 Series Holder
When you have a heavy-duty rotary broaching application, these adjustable center Rotary Broach holders are very capable and built with Swiss precision. Already well known in Europe, PCM®'s Rotary Broach holders are some of the finest available to the machining industry. Capable of making a hex broach anywhere from .040"- 1⅛", these broach holders have a wide range of capabilities and uses. Ideal for CNC Machining Centers, Turning Centers, or Rotary Transfer Machines where center locating is required to get an accurate broach.
- Hex cap screws enable easier locking of adjustment settings
- Four quadrant micro adjustability enables easiest center locating for better broach results
- Adjustable broaching holder designed for CNC Lathes & Turning centers
- Can be adapted with a special die to produce external broach forms such as splines
- Max thrust force: 2700lbs
- Uses 8mm shank broaches
6190 / 6191 Series Holder
This unit is intended for larger machinery and uses larger diameter shank broach tools. Internally this unit features an extremely robust bearing back that can withstand up to 9000lbs of axial pressure. Holds 6150 Series broaches.
- Adjustable broaching holder designed for the largest of turning centers and CNC lathes
- This broaching holder features a robust bearing configuration to withstand the high forces required to attain some of the largest of broach profiles
- Max thrust force: 9000lbs
- Uses 12mm shank broaches
Static Punch Holder
When special ID forms are required on your Swiss-style machining jobs, look to our static punch broach holders for ease of use, repeatability and rigidity. Our holders are able to position a broach form tool at a known location for timing or positioning of the broached profile.
Partial forms are available by quote on request. Call 413-562-4800 to talk live with one of our technical experts about your application. Quick turnaround time on tools made from standard 8x28mm blanks.
ROTARY BROACH TOOLS
Each broach is machined from a proprietary material for use in alloys commonly machined in the medical industry. Broach tools can be used with any holder that accepts an 8-mm shank size for use in Swiss-type CNC machines, CNC lathers and turning centers.
The broach is held in a broach holder that enables the broach to rotate at the same speed as the part, and the machine simply pushes the broach forward to create the shape. The most common broach tools are push broaches used to create square and hexagonal holes and internal keyways. Because the tools are self-supporting, a simple hand-operated arbor press can be used to push the broach through the workpiece.
Special sizes available upon request. Quick turnaround time.
Signature Series Hexagon Broaches - 1¼ inch OAL
Signature Series Hexagon Broaches - 28mm OAL
2110 Series Hexagon Broaches - HiCo8 Grade (use with 2160 & 6180)
2122 Series Hexalobular Broach Tools (use with 2160 & 6180)
2151 Series Broach Tools (use with 2150 Series Micro Broach Holder)
6150 Series Hexagon Broaches - HiCo8 Grade
GenSwiss’ premium rotary broaching tools and rotary broach holders deliver consistent high-performance cutting for industries requiring the highest degree of standards.
![]() |
Rotary Broach 2160 Holder & Broach Tools are the part of the GenSwiss® Signature Series Line of Premium Products made in the USA. Standard and custom orders are available. We strive to deliver products which meet or exceed customer expectations, providing a reliable service with application solutions. Contact us for more information 1-413-562-4800 |